جوش لیزری فلزات نامشابه، مثل جوش دادن مس به آلومینیوم یا مس به آهن ضد زنگ، همیشه با چالشهای زیادی روبرو بوده است اما در حال حاضر بیش از پیش به این نوع جوشکاریها نیاز است زیرا در حوزه خودرو و وسایل الکترونیکی زیاد استفاده می شود. مثالی معمولی در این حوزه، جوش لیزری سیم هادی مسی به اجزای آلومینیومی یا آهنی باتری است. این مقاله در واقع آزمایشی در کوهیرینت واقع در سانتاکلارا کالیفرنیا بر اساس فناوری اسمارتولدپلاس (SmartWeld+) شرکت است که میخواهد توان تولید این نوع جوشهای لیزری با کیفیت و ظرفیتهای بالا را که با نیازهای حوزه تولید وسایل الکترونیکی و خودروها سازگار است، نشان دهد.
چالش جوشکاری مواد متفاوت
در مورد کارکرد جوش سیم هادی در حوزه خودروهای الکترونیکی، نیاز است موارد زیر را بدانید. اول اینکه جوش لیزری باید رسانایی حرارتی و الکتریکی خوبی داشته باشد، هر گونه اغماض و کوتاهی در این مورد، بهخصوص در مورد رسانایی الکتریکی، باعث کاهش برد ماشین، افزایش فرکانس شارژ و بالا رفتن هزینههای ماشین میشود؛ تمامی اینها هم خروجیهای نامطلوبی هستند. علاوه بر این ها جوشکاری سیم هادی باید از قدرت مکانیکی بسیار بالایی برخوردار باشد، چرا که استفاده از این ابزار در اتومبیل باعث میشود این تجهیزات در معرض لرزههای مداوم و شوکهای ناگهانی قرار بگیرند.
وقتی جوش لیزری در حال جوش دادن مواد مشابه یا یکسان باشد، یک پیوند متالورژی کامل در خط جوش به وجود میآید. یعنی، محل جوشکاری شده همان ترکیبات فلزی را دارد و در بهترین حالت از خصوصیات مکانیکی مشابه (برای مثال، قدرت کششی، نرمی و سایر موارد) با ماده یا مواد اصلی برخوردار است. در بعضی موارد، مواد ناهمسان آلیاژهای باثباتی شکل میدهند که وضعیت مطلوبی دارند؛ مثلا ترکیب مس و زینک، آلیاژ برنج ایجاد میکند. اما، بسیاری از مواد دیگر یا از نظر متالورژی آلیاژهای باثباتی ایجاد نمیکنند و یا آلیاژهای قابل قبولی ندارند.
در صورتی که یک پیوند متالورژی کامل بین مواد مورد استفاده ایجاد نشود، تنها راه ایجاد یک «حصار» مکانیکی است؛ بدین صورت که ترکیبی فضایی از آلیاژهای ناهمسان ایجاد میکنیم تا بتوانند به صورت فیزیکی به گونهای کنار هم قرار بگیرند که از قدرت مکانیکی کافی برای متصل شدن بهم برخوردار شوند. این حالت مثل ایجاد مجموعهای از «میخهای» در هم پیچیده در ماده است که داخل هم نفوذ کرده و جوش را نگه میدارند.
یک راه برای ایجاد این نوع اتصال مکانیکی فشار فیزیکی دو قطعه بهم و بعد استفاده از پالسهای لیزری برای ذوب کردن دو ماده به شکل نقطهای و سه بعدی است. اما، با این رویکرد در نهایت هیچ کنترلی روی پویایی محل ذوب نیست و همین موجب میشود که کیفیت سطح رضایتبخش نباشد ولی با ایجاد تعداد زیادی از این تکهها، میتوان به سادگی به یک اتصال مکانیکی خوب دست پیدا کرد اما نتیجه این فرآیند کاملا یکدست و مقاوم نیست.جوش لحیم قدیمی هم برای استفاده در حوزه خودروهای الکتریکی عامل معیوبی به شمار میرود، چرا که اتصالات لحیمکاری شده نقطه ذوب پایینی دارند و قدرت و ثبات مکانیکی چندانی ندارند. علاوه بر این، جوش لحیم اغلب حاوی سرب است که موجب نگرانیهایی در مورد محیط زیست میشود.
کنترل اشعه لیزری
بیشتر موارد جوشکاری لیزری فایبر روی نقاط بزرگتر، چندحالتی و متمرکز صورت میگیرد. این کار موجب از بین رفتن مشکل ایجاد خط جوش بسیار باریکی میشود که قدرت مکانیکی چندانی ندارد. اما، حتی نقطه لیزر چندحالتی هم هنوز به شکاف فیزیکی نسبتا ریزی بین قطعات نیاز دارد که باعث میشود تولید کننده از روی ضرورت، لبه قطعات و تجهیزات خود را با دقت بیشتری استفاده نماید. تمام این ملزومات همگی باعث افزایش هزینه تولید میشوند.
تا کنون اشعه لرزشی یا تابدار یا همان پرتوی سریع یک خط عمودی اشعه لیزری کوچک، متمرکز در حالت تکی یا چندتایی روی خط جوش (به جای استفاده از حرکت خط صاف ساده اشعه روی خط جوش مد نظر) به عنوان ابزاری برای فائق آمدن بر این محدودیتها شناخته شده است. اشعه لرزشی باعث افزایش اندازه مؤثر اشعه شده و در عین حال قدرت لیزری لازم را با شدت مطلوب به سوراخ جوش مورد نظر میتاباند. به این ترتیب، اشعه لرزشی بین شکافهای نسبتا بزرگ را پوشانده و پارامترهای جوش که شامل پهنای خط جوش و عمق نفوذ جوش می شوند را با کنترل بهتر و مطمئنتری فراهم میکند. در چندین مورد، استفاده از اشعه لرزشی با نقطه یک یا چندگانه نسبت به جوش چندحالتی قدیمی نتایجی عالی داشته است.
استفاده خاص کوهیرینت از کنترل اشعه با نام اسمارتولدپلاس، نسبت به سایر نسخههای این روش از مزایای زیادی برخوردار است بهخصوص که ورودی انرژی این روش کنترل اشعه قابل پیشبینی است. این کنترل با اشعه مادونسرخ (۱۰۷۰ نانومتری) متمرکز و تکی با اندازه نقطهای ۳۰ µm کار میکند و الگوهای نوسانی متعدد و متنوعی را که شامل بیضیها، حلزونیها و حتی الگوهایی پیچیدهتر است (شکل ۱) میتواند ایجاد کند. این الگوها را میتوان در اندازههای مختلف درآورد و به صورت خودکار گرداند تا مسیر یا خط تراز جوش خاصی را دنبال کند. توزیع انرژی را میتوان در یک نقطه یا خط با تنظیم سرعت تابش در راستای مسیری درون یک الگوی کوچکتر به طور دقیق کنترل کرد و در مواردی میتوان قدرت اشعه را هم تنظیم کرد.
این موضوع این امکان را فراهم می آورد که در بخشهای مختلف یک الگو یا ماده ورودی انرژی را تنظیم کرد و محیطهایی با حرارت مقدماتی، فرآوری یا سرد شده تعریف کرد و حرکت و پویایی محل جوش را به دقت دستکاری کرد. نتیجه این امر هم بهبود دقت و تکرار شوندگی جوش، کوچک کردن محل حرارت دیده و کمتر شدن خلل و فرج است. مثالهایی که اینجا آورده شده مزایای خاص این تکنیک را نشان میدهند.
نتیجه جوش سیم هادی و رابط
سیگمکلد (SIGMAclad) یک ورق لمینت متشکل از چند ماده است که بهطور خاص برای استفاده به عنوان یک رابط الکتریکی در مواردی مثل خودروهای برقی طراحی شده است. این ورق طراحی شد تا جای نیکل را بگیرد که پیشتر برای اتصال باتریهای لیتیوم-یونی به کار میرفت. با اینکه نیکل از ترکیبی مطلوب از خصوصیات مکانیکی، شیمیایی و الکتریکی برخوردار است، مقاومت الکتریکی آن باعث ایجاد حرارت میشود و به همین ترتیب کارایی آن هم کاهش پیدا میکند. سیگمکلد ورقی پنج لایه از مواد مختلف شامل نیکل، آهن ضد زنگ، مس، آهن ضد زنگ و نیکل است.
اخیرا در تحقیقی کنترل شده با استفاده از اسمارتولدپلاس (در شکل ۲)، دو تست جوش با سیگمکلد انجام شده است. در تست اول که جوش سیم هادی به یک سیم هادی همجوار آزمایش شده است، یک سیم هادی سیگمکلد ۰.۳ میلیمتری به یک نوار از همین جنس با همان ضخامت و بدون لایه مسی دوم، جوش خورده است. در تست بعدی که فرآیند اتصال یک باتری سیلندری به یک سیم هادی مورد آزمایش قرار گرفته است، نواری از جنس سیگمکلد به یک ورق مسی نیکل اندود شده یک میلیمتری، جوش داده شد.
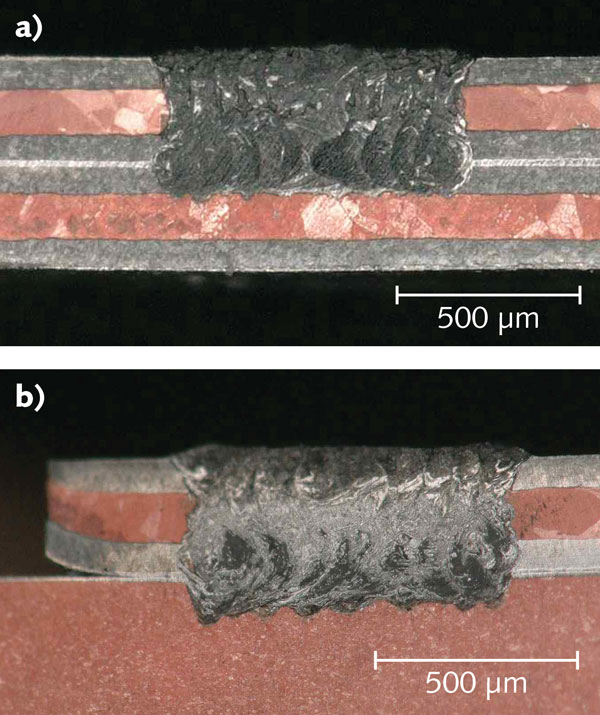
در هر دو جوش، ۱۵۰ تا ۳۵۰ وات قدرت لیزری استفاده شده و اشعه با الگویی ریزحلزونی تابیده شده است. کل خط جوش قطری ۱ میلیمتری و عمقی ۴۰۰ µm داشت. جوش دادن ۴۰ میکروثانیه طول کشید تا بتواند نقطه جوشی با قطر ۱ میلیمتر ایجاد کند.
تصاویر شکل ۲ برش عرضی از دو جوش را نشان میدهد. در هر دو مورد، جوشها از برش عرضی با زاویههای قائمهای برخوردار هستند و پیوندهای قوی و یکدستی دارند. علاوه بر این، نقاط جوشکاری شده عمق خوبی دارند که در مورد اتصال دو سیم هادی، این عمق در لایه مسی دوم در بهترین میزان قرار دارد. موارد گفته شده نتایج مستقیم کنترل دقیق ورودی انرژی روی فضا و زمان هستند.
مجموعه دیگری از این تستها با استفاده از جوش سه ورق مسی نیکل اندود با ضخامت ۰.۲ میلیمتری به آلومینیوم با استفاده از قدرت لیزری ۵۰۰ واتی صورت گرفت (شکل ۳). الگوی لرزشی یا تابداری که در این مورد استفاده شده به شکل «بینهایت» یا عدد ۸ بوده که نسبت طول و عرض آن را میتوان نسبت به سرعت مورد استفاده تنظیم کرد. پهنای خط جوش در نواری با طول ۲۰ میلیمتر، ۱.۴ میلیمتر بوده است و ۰.۶ ثانیه طول کشیده تا این جوش با عمق ۱ میلیمتر ایجاد شود.
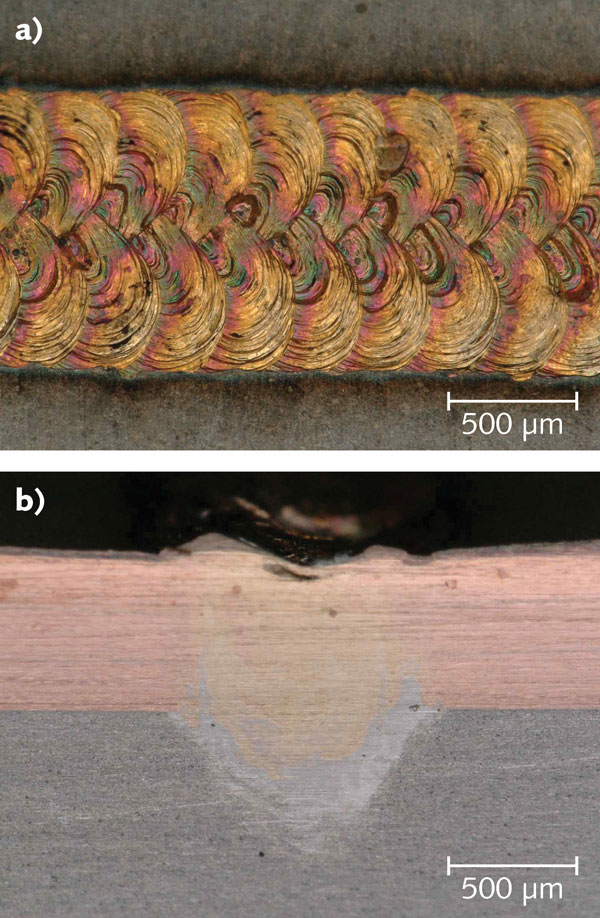
شکل ۳ نمایی از بالا و برش عرضی این جوش را نشان میدهد. مجددا، این جوش تجانس متالورژی عالی (یا تخلل پایین) داشته و لایه بالایی تیز بسیار کمی پیدا کرده است و پشت ورقه آلومینیومی اثری از جوش دیده نمیشود. در تست مکانیکی، مقاومت برشی بیش از ۱۷۰۰ N برای این جوش تخمین زده شد.
در تحقیق سوم (شکل ۴) نوع جوش نقطهای که تولید کنندههای باتری اغلب برای اتصال الکتریکی به یک پیل به آن نیاز دارند، نشان داده شده است. برای این کار، نوار مسی با ضخامت ۰.۲ میلیمتری به یک آهن ضد زنگ با ضخامت ۰.۳ میلیمتری (که معمولا برای روکش سیلندری باتری از آن استفاده میشود) جوش زده شده است. در اینجا، از لیزری با قدرت ۵۰۰ وات استفاده شده و اشعه به شکل حلزونی تابیده شد است. نقطه پایانی جوش خورده ۱ میلیمتر قطر و عمقی حدود ۳۰۰ µm داشت و ۲۶ میکروثانیه طول کشید تا این جوش زده شود.
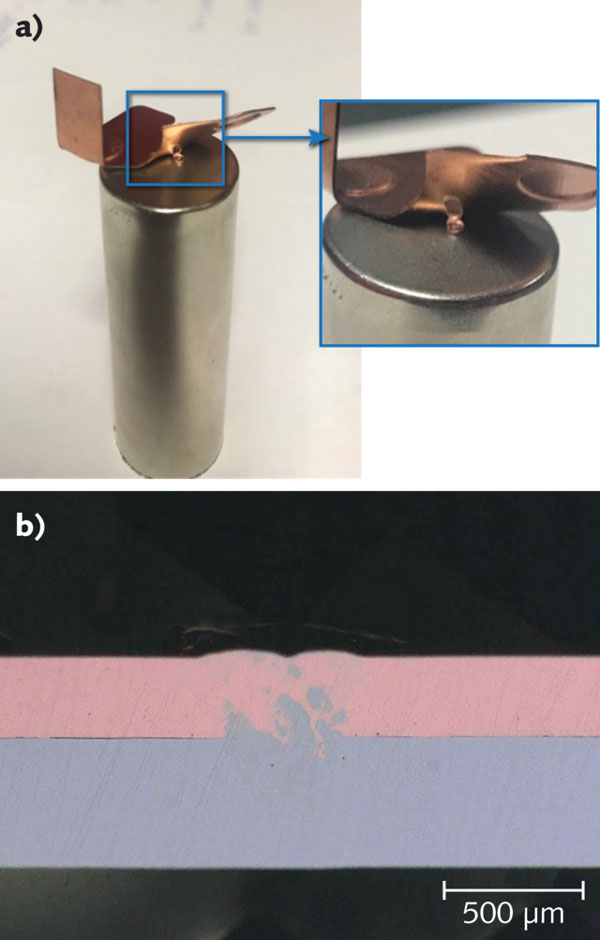
تصاویر شکل ۴ نشان میدهند که با استفاده از این پارامترهای فرآوری، به ترکیبی کافی از مواد دست پیدا کردهاند. جوش هم از رسانایی الکتریکی بالا و مقاومت برشی ۱۵۰ N در هر نقطه جوش برخوردار بوده است.
علاوه بر این، درون پیل باتری اثری از حرارت جوش دیده نشده است و دلیل این امر را می توان در کنترل دقیق ورودی انرژی یافت. این امر در مورد باتری از اهمیت بسیار بالایی برخوردار است، چرا که جعبههای تقسیم بعد از اینکه پر از الکترولیت میشوند، بهم متصل میشوند. حرارت وارده میتواند باعث آسیب دیدن سلول یا پیل لیتیوم-یونی شده و منفجر شود.
جمعبندی
کنترل دقیق اشعه با استفاده از اسمارتولدپلاس پیشرفتی شگرف در حوزه فناوری جوش لیزری فایبر بوده و موجب شده این تجهیزات لیزری بهصرفه و قابل اتکا در حوزههای متعددی به کار گرفته شوند. حال، کنترل اشعه از اشعههای نوسانی گرد ساده عبور کرده و الگوهای جوش زیادی را میتواند دربربگیرد و قدرت لیزر را به شکل پیچیدهتری کنترل کند. این توانایی بهخصوص زمانی که با سیستمهای گازرسانی نوآورانه همراه میشود، کنترل بیشتری روی پویایی و حرکت محل ذوب ایجاد میکند و جوشهای باکیفیتتر و مطمئنتری ایجاد میکند. تمامی این موارد باعث میشود جوش مواد ناهمسان و ورقههای ظریف کیفیت بیشتری پیدا کنند و بتوان در تولیدات الکترونیکی و خودروهای برقی، جوشکاریهای چالشبرانگیز دیگر را هم انجام داد.